Common local practice is to support structures on one foundation system. An example would be deep piles to support a pile cap and grade beam substructure. Another example would be shallow footings bearing on a subgrade improved with Geopier® ground improvement. The general logic is that sticking with one foundation type helps limit potential differential settlement across the structure. For most projects, having one foundation system is a foregone conclusion since subsurface soil conditions below a given footprint generally have some level of consistency and require the same foundation type.
However, some sites have relatively drastic changes in subsurface soil conditions across a proposed building footprint. Or there could be other factors, such as access limitations, that make a mixed foundation scheme an attractive solution.
Below are some project examples where mixed foundation systems were used. They all have one thing in common – they were engineered to limit differential settlement between the two different foundation support areas. The building doesn’t “care” that it has two foundation types provided that they are designed for minimal differential settlement. With proper planning and engineering, it can be done!
Featured Projects
India Street Residential, Portland, ME
- Foundation System #1 – Geopier GeoConcrete® Column Rigid Inclusions
- Foundation System #2 – Ductile Iron Piles
Figure 1 – Ductile Iron Piles are installed at a safe distance from active power lines.
The India Street Residential project was planned for Geopier GeoConcrete Column (GCC) Rigid Inclusion Ground Improvement to support a conventional shallow footing foundation system. During project planning, the project team identified an overhead utility line along the perimeter of the site that would require relocation to facilitate the safe installation of the GCCs with a long, vertical mast rig. As the project schedule continued to advance towards construction, relocation of the utility line was delayed by the power company and threatened the overall project schedule. We worked with the project team on a foundation alternative within the area of the utility line conflict that consisted of Ductile Iron Piles (DIPs). DIPs are installed in 16.5-foot-long segments with an excavator-mounted hammer and can work within limited overhead environments. This enabled the installation of piles for support of foundations immediately adjacent to the active power lines, while the remainder of the project was supported by Geopier GCC Rigid Inclusions as originally planned.
Boston Post Road Residential, Wayland, MA
- Foundation System #1 – Footings on Natural Soils
- Foundation System #2 – Footings on Geopier Rammed Aggregate Pier® Element Improved Soils.
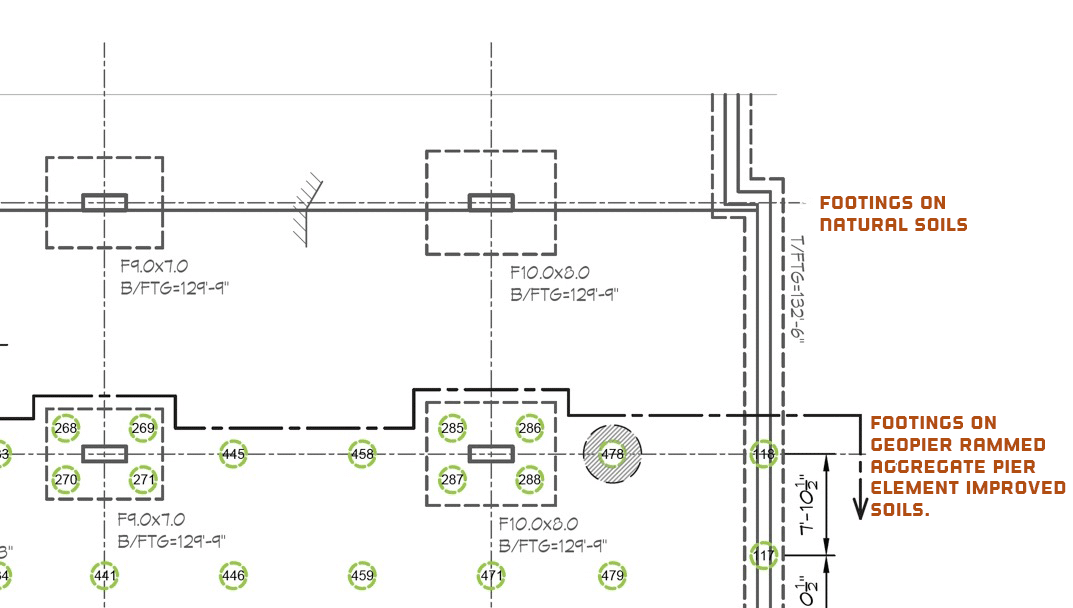
Figure 2 – A ground improvement design drawing shows footings supported on natural soils and Geopier RAP- improved soils.
The project consisted of a 4-story residential structure. Most of the building area was underlain by natural granular soils at shallow depths. In these areas, supporting the building on conventional shallow footings and a slab-on-grade (all bearing on natural granular soils) was the most cost-effective approach. However, about 25,000 square feet of the proposed footprint was underlain by about 10 feet of unsuitable fill. Rather than removing and replacing the unsuitable fill, the project team requested a Geopier Rammed Aggregate Pier (RAP) ground improvement solution in this area. The RAP solution provided an improved subgrade for conventional footing and slab-on-grade support. Thus, most of the footings and slabs were supported on natural soils and about one-third were supported on Geopier RAP-improved ground.
Methuen Construction Headquarters Building Addition, Plaistow, NH
- Foundation System #1 – Geopier Rammed Aggregate Pier® Elements
- Foundation System #2 – Ductile Iron Piles
Figure 3 – Ductile Iron Piles are installed within an existing building.
Support of this single-story building addition over loose/soft soils was most cost-effectively addressed using Geopier Rammed Aggregate Pier (RAP) ground improvement. However, interior portions of the renovation work as well as limited exterior construction immediately adjacent to existing aging exterior masonry block walls required alternate construction approaches. We worked closely with the project team to evaluate multiple foundation support technologies including Helical Piles, Drilled Micropiles and Ductile Iron Piles (DIPs). Ultimately, a solution was selected that combined low vibration, modular DIPs at interior locations and along existing exterior walls, with Geopier RAP ground improvement for the main addition.